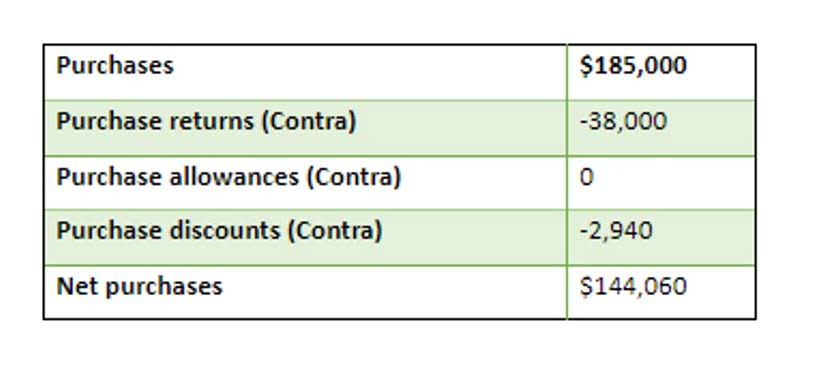
Increasing or improving your profitability depends on how much you spend on manufacturing. MRPeasy is a cloud ERP software that focuses on the small manufacturing industry. This solution combines sales, materials planning, shop floor reporting, production scheduling, inventory management, and procurement into one place.
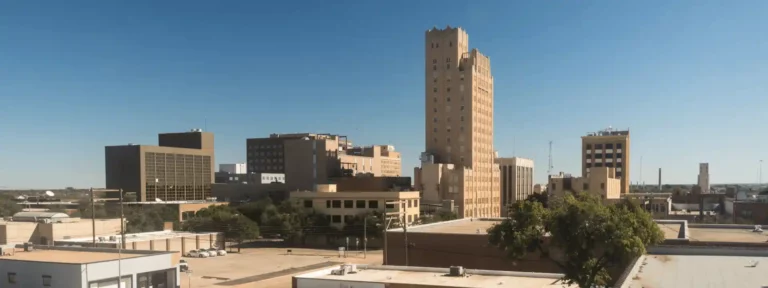
Understanding the Costs in Product Costs
- These costs are necessary for the overall operation of the factory, but they cannot be directly traced to each unit of production.
- When reviewing manufacturing overhead, it is essential to consider what’s included.
- To effectively determine the total overhead costs incurred, companies must first aggregate all indirect costs.
- All three types of overheads – fixed, variable, and semivariable – are essential for businesses to understand in order to accurately calculate the cost of production.
- Other examples include legal fees and administrative expenses, transport fuel, and wages for seasonal work.
- Whatever quantity of goods the company produces, these overhead costs do not change.
- In a good month, Tillery produces 100 shoes with indirect costs for each shoe at $10 apiece.
If you’re trying to improve your manufacturing overhead rate, for example, keeping a close eye on this data will help you identify what efforts are working. Manufacturing overhead is made up of the indirect costs a company undertakes in its production process. Other expenses such as direct labor hours, materials costs, and similar items directly involved in the actual manufacturing process, do not fall under the category of manufacturing overhead. Understanding and calculating manufacturing overhead costs is pivotal for any manufacturing business aiming to get a realistic picture of their production expenses. Unlike direct costs, which can be tied to the production of specific goods, overhead costs are indirect and cannot be directly attributed to a specific product. Knowing how to accurately estimate these costs is essential for setting product prices, budgeting, and maintaining profitability.
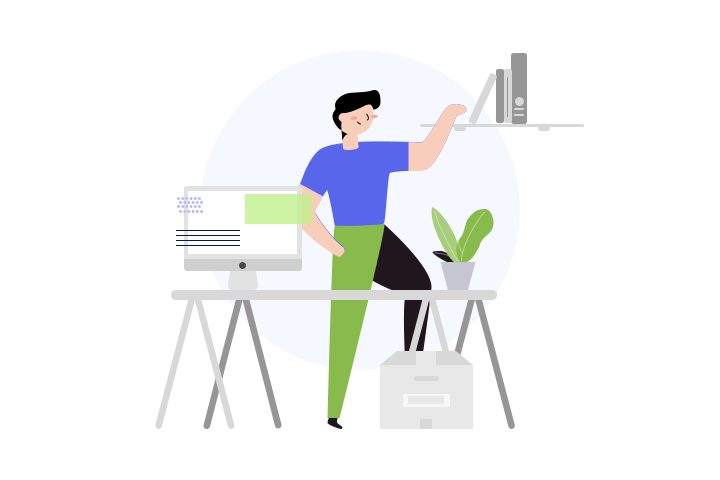
Best Manufacturing Execution Systems for Singaporean Businesses in 2024
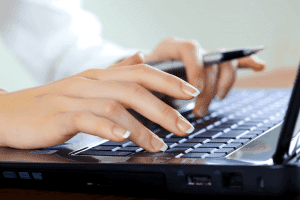
In fact, KPMG LLP was the first of the Big Four firms to organize itself along the same industry lines as clients. Take your learning and productivity to the next level with our Premium Templates. Keeping track of tax deductions quickly becomes routine, once you’re familiar with what can and can’t be deducted.
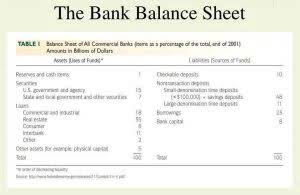
Predetermined Manufacturing Overhead Rate Formula
- A company must pay overhead on an ongoing basis, regardless of how much or how little the company sells.
- As technology continues to develop, we can expect to see even more innovative ways to reduce manufacturing overhead costs.
- ABC assigns costs to products based on the actual activities required for their production, thereby linking expenses to the consumption of resources more directly.
- These costs are then charged to the cost of goods sold as the units are sold over time.
- Add up all the indirect costs that make the production process run smoothly each month.
- Manufacturing overhead is also known as factory overheads or manufacturing support costs.
According to a study conducted by McKinsey, these indirect costs account for 8% to 12% of the overall manufacturing costs. Keep in mind that you don't have to calculate the manufacturing overhead for a single unit to keep accurate books. While some companies find that helpful for different aspects of accounting, such as pricing, it's not necessary.
Manufacturing Overhead Costs
- In addition, a Computerized Maintenance Management System helps you maintain a broad view of your entire operations.
- It might buy you some time before you need to spend all that money on a new piece of equipment.
- As a result, manufacturing overhead costs are a part of the industry, and you cannot predict how much it will be.
- You can find the overhead rate of your manufacturing operations using the following formula.
- Inventory serves as a buffer between 1) a company’s sales of goods, and 2) its purchases or production of goods.
- For the past 52 years, Harold Averkamp (CPA, MBA) has worked as an accounting supervisor, manager, consultant, university instructor, and innovator in teaching accounting online.
In our research and experience, we’ve found eight specific ways for companies to reduce manufacturing overhead. Here are some frequently asked questions (FAQs) and answers that address key concepts related to manufacturing costs. Manufacturers can compare the costs of making a product using different manufacturing processes. This helps them understand the most efficient process and the investment they need to make for the selected process. With a breakup of all the costs of manufacturing, management can decide whether it is more profitable to purchase certain parts or materials from a vendor or manufacture them in-house. For instance, if some raw materials are driving up costs, manufacturers can negotiate with other suppliers who may be willing to supply these materials at a lower cost.
Costs on Financial Statements
If, for instance, 2,500 machine hours were logged in a given month, the company would allocate $40 per machine hour ($100,000 ÷ 2,500 hours). A low manufacturing overhead rate signifies is shipping cost manufacturing overhead efficient and effective resource utilization within your business. However, a higher rate may suggest your production process is experiencing delays or inefficiencies.
- Manufacturing overhead refers to indirect costs a company or manufacturer incurs during production.
- These costs can be fixed, such as rent, or variable, such as transport costs.
- By following the tips outlined above, manufacturers can more effectively manage their manufacturing overhead costs and improve their bottom line.
- You can also track non-human resources, such as equipment, suppliers and more.
- Once you set a baseline to capture your schedule, planned costs and actual costs can be compared to ensure you’re keeping to your budget.
- Contrary to direct costs like raw materials and labor, which align closely with production volumes, overhead costs can be less apparent yet crucial for the overall budget health.